Lean Manufacturing e logistica di magazzino: basta sprechi
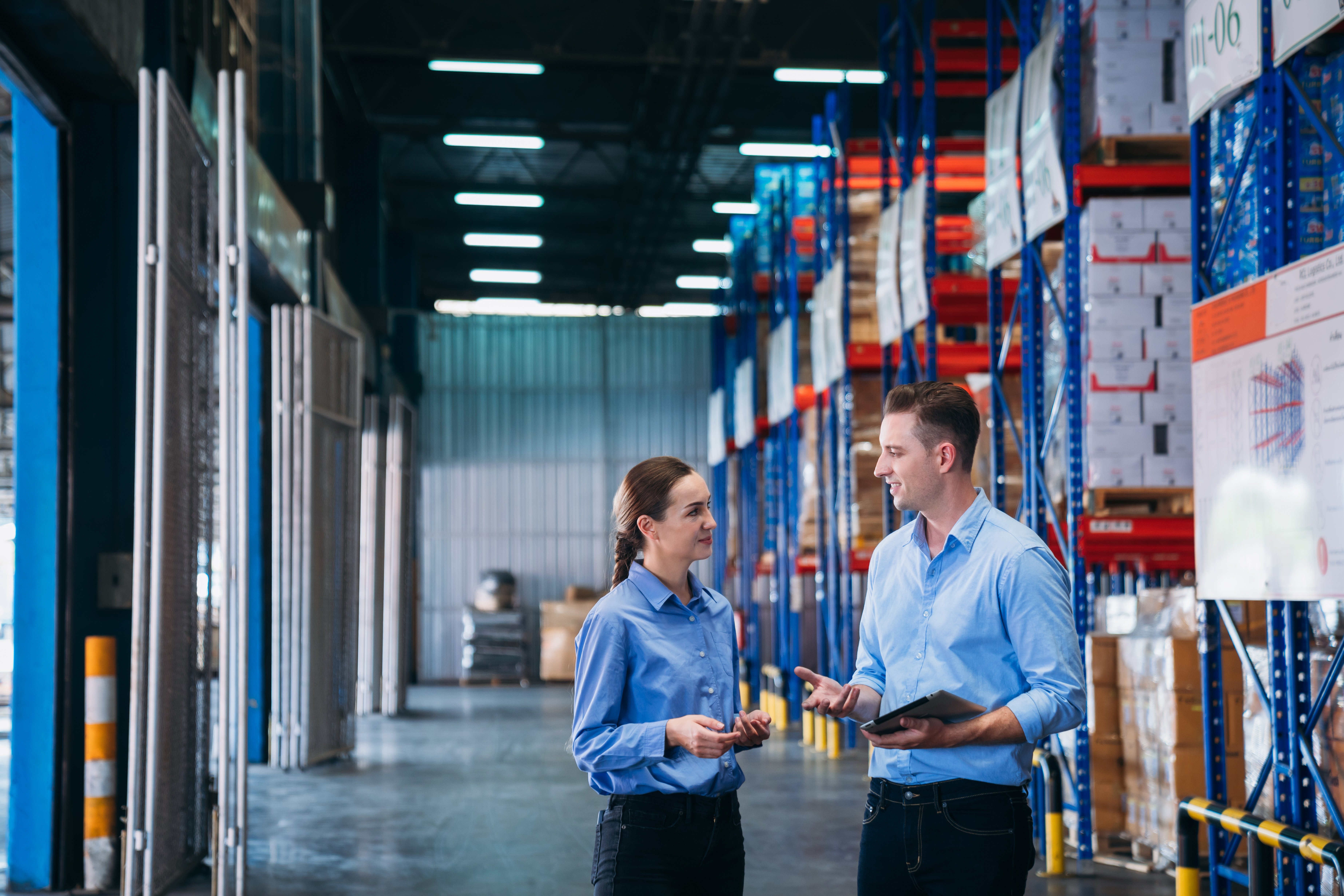
In un mondo in cui l’efficienza è la chiave del successo, le aziende sono costantemente alla ricerca di metodi per ottimizzare i loro processi di magazzino. Questa ricerca è alimentata dalla necessità di rimanere competitivi in un mercato globalizzato, dove la velocità, la precisione e la qualità del servizio possono fare la differenza. In questo contesto, il Lean Manufacturing emerge come una strategia vincente. Questo approccio, nato in Giappone e perfezionato nel corso degli anni, si concentra sulla riduzione degli sprechi in tutte le sue forme e sull’aumento della produttività, puntando a creare un sistema di produzione snello ed efficiente.
Ma cos’è esattamente il Lean Manufacturing e perché è così importante per le aziende di oggi?
Cos’è il Lean Manufacturing e perché è importante
Il Lean Manufacturing è un approccio alla gestione del magazzino che si concentra sull’eliminazione degli sprechi e offre prodotti di alta qualità su richiesta del cliente. Questo approccio ha origine dal Sistema di Produzione Toyota (TPS), un modello di produzione giapponese basato sulla continua eliminazione degli sprechi. Il TPS valorizza concetti come il “just-in-time” e il “jidoka”, oggi la base del Lean Manufacturing. Quest’ultimo è una filosofia che coinvolge l’intera organizzazione, dal top management ai lavoratori di linea.
I principi fondamentali del Lean Manufacturing includono:
-
riduzione degli sprechi;
-
ottimizzazione del flusso di lavoro;
-
creazione di valore per il cliente;
-
adozione di un approccio di miglioramento continuo in cui tutte le risorse sono coinvolte nell’identificazione e nella risoluzione dei problemi
Come funziona il Lean Manufacturing nella logistica di magazzino
Nella logistica di magazzino, il Lean Manufacturing si traduce nell’adozione di strumenti, tecniche e tecnologie specifiche che consentono di creare un ambiente di lavoro più produttivo e redditizio.
A supporto del Lean Manufacturing possono essere implementati diversi sistemi, metodi e tecnologie, tra cui:
-
5S. Il 5S è un sistema per organizzare e mantenere un ambiente di lavoro pulito ed efficiente. Questo sistema, che prende il nome da cinque parole giapponesi che in lingua inglese si traducono con: Sort, Set in order, Shine, Standardize e Sustain, aiuta a creare un ambiente di lavoro che promuove l’efficienza e la sicurezza. Nella logistica di magazzino, il 5S può essere utilizzato per organizzare gli spazi di lavoro, migliorare la visibilità degli articoli e ridurre il tempo necessario per trovare e recuperare gli articoli.
-
Kanban. Il Kanban è un sistema di schedulazione visuale che indica quando produrre e trasportare gli articoli. Può essere utilizzato per gestire l’inventario e assicurare che gli articoli siano prodotti e trasportati al momento giusto, riducendo così gli sprechi e migliorando l’efficienza.
-
Just-in-Time (JIT). Il JIT è un sistema di produzione che mira a ridurre i tempi di attesa e i livelli di inventario. È utile per sincronizzare la produzione e la consegna degli articoli, assicurando che gli articoli siano prodotti solo quando necessario e riducendo così gli sprechi di inventario.
-
Heijunka. L’Heijunka è un sistema di livellamento della produzione per ridurre le fluttuazioni nel carico di lavoro. Permette di bilanciare il carico di lavoro tra i diversi turni e i diversi membri del team.
-
Jidoka. Il Jidoka è un approccio che prevede l’arresto del processo di produzione non appena viene rilevato un problema.
Alla base del sistema di gestione di magazzino, però, è necessario che ci sia un buon Warehouse Management System (WMS. Il WMS può supportare l’implementazione del Lean Manufacturing, fornendo strumenti per ottimizzare la gestione dell’inventario, ridurre gli sprechi e rivedere i processi logistici per utilizzare nel migliore dei modi ogni risorsa disponibile
Ricezione merce, stoccaggio, picking e spedizione con le metodologie di Lean Manufacturing
L’applicazione delle metodologie di Lean Manufacturing può portare a miglioramenti significativi nei processi di ricezione, stoccaggio, picking e spedizione, processi cruciali all’interno delle logiche di magazzino. Ottimizzare tali attività risulta strategico al fine di aumentare l’efficienza e ridurre sprechi di tempo e risorse.
Nello specifico:
-
Nella fase di ricezione merce, l’obiettivo del Lean Manufacturing è migliorare l’efficienza e l’accuratezza del processo attraverso l’implementazione di procedure standardizzate per la ricezione delle merci. In questo caso, le etichette RFID (Radio Frequency Identification) permettono un tracciamento preciso e in tempo reale delle merci in ingresso. Inoltre, gli AGV (Automated Guided Vehicles) possono essere utilizzati per trasportare le merci in modo efficiente all’interno del magazzino, riducendo il tempo e l’effort fisico del personale.
-
Nella fase di stoccaggio, le tecniche di Lean Manufacturing come il 5S (Sort, Set in order, Shine, Standardize, Sustain) possono essere utilizzate per mantenere l’ordine e l’efficienza nel magazzino. Inoltre, l’uso di sistemi di stoccaggio verticali, come le scaffalature alte, massimizza lo spazio disponibile.
-
Nella fase di picking, è possibile aumentare l’efficienza del processo attraverso l’uso di tecniche come il picking per zona e il picking per onda. Queste tecniche riducono il tempo necessario per raccogliere un ordine e minimizzano gli errori. Infine, l’uso di sistemi di voice picking o pick-to-light permette di aumentare l'agilità nelle procedure di prelievo e consente agli operatori di lavorare in modo efficiente, mantenendo le mani libere per il prelievo degli articoli.
-
Nella fase finale di spedizione, è possibile introdurre tecnologie per il tracciamento in tempo reale degli articoli e automatizzare il processo di imballaggio.
Questo approccio offre, dunque, un insieme di strumenti e tecniche che, se implementati correttamente, possono trasformare le operazioni di magazzino, migliorare l’efficienza e la produttività, e infine portare a un vantaggio competitivo sostenibile. Tuttavia, è bene tenere a mente che la sua implementazione richiede un impegno costante e una cultura volta al continuo, condivisa da tutta l’organizzazione.