Magazzini automatizzati: un modello per l’ottimizzazione del riposizionamento merci
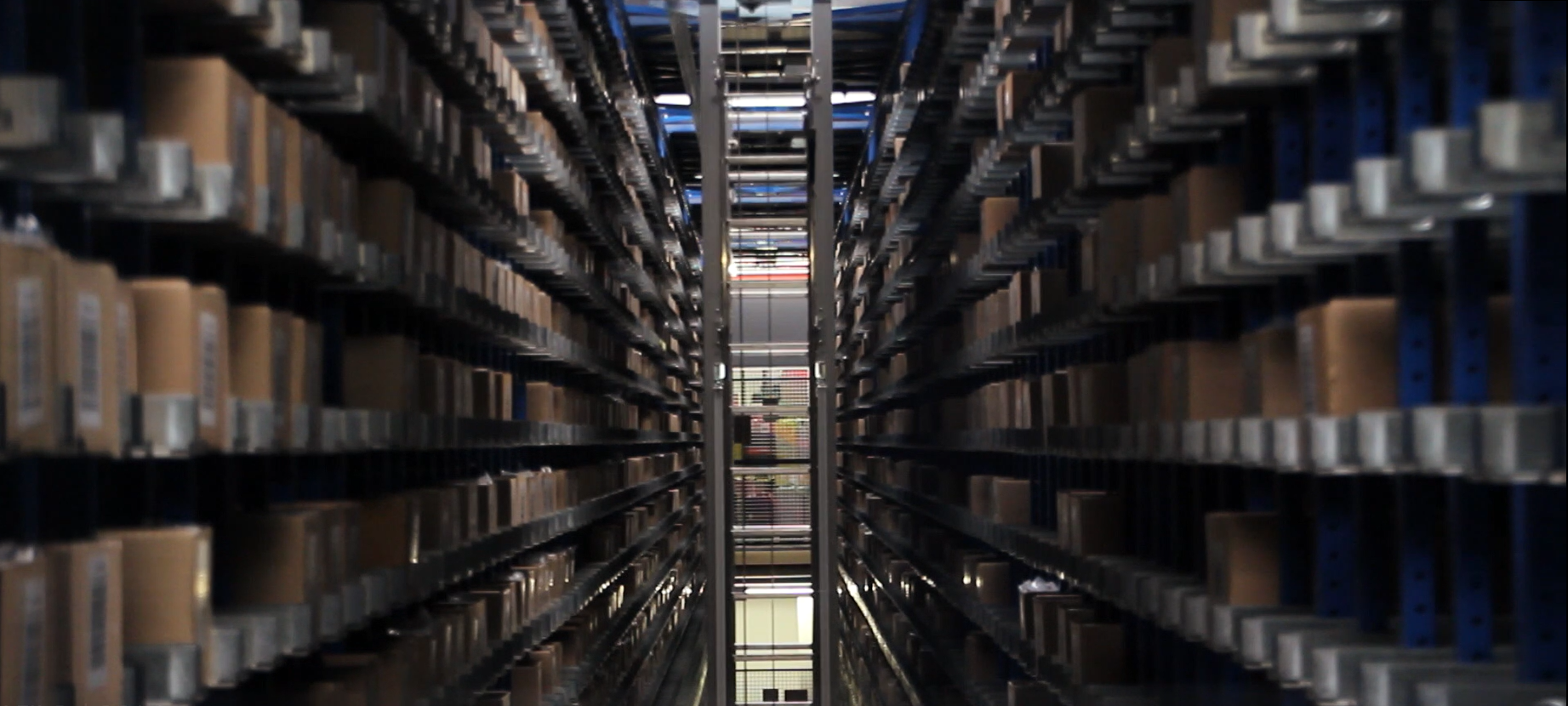
Oggi, la qualità e il prezzo del prodotto non bastano ad essere competitivi, è, infatti, necessario offrire al cliente un ottimo servizio, caratterizzato da puntualità e frequenza delle consegne.
Di conseguenza, il ruolo della logistica all’interno delle strategie aziendali è divenuto sempre più importante: chi primeggia in quest’ambito ha maggiori possibilità di essere competitivo nel mercato globale. Per raggiungere quest’obiettivo, la gestione del magazzino diviene un elemento determinante e, nel caso dei magazzini automatizzati, un valido modello di riposizionamento merci può fare la differenza in termini di costi, time-saving ed efficienza.
Il magazzino, centro operativo dell’azienda
Il magazzino è, infatti, il centro operativo dell’azienda, il luogo in cui si svolge la maggior parte dell’attività logistica. Qui non solo la merce viene ricevuta, posizionata, custodita e spedita, ma transitano valori economici, strategici e promozionali. Il magazzino è il polmone dell’azienda.
Questo, infatti, incide in modo significativo sui costi sostenuti e sul livello di servizio espresso nei confronti dei clienti. Una buona gestione del magazzino può portare a:
-riduzione degli spazi di stoccaggio
-riduzione dei costi
-ottimizzazione dei tempi di movimentazione e di evasione degli articoli
-aumento della competitività.
Sono numerose le attività che animano la vita di un magazzino e tra queste, la più costosa in termini di tempo e denaro è sicuramente il picking, ovvero la selezione, il prelievo parziale e il raggruppamento delle unità di carico da spedire al cliente.
L’ottimizzazione della disposizione, cioè lo spazio da assegnare ad ogni unità di carico, è un elemento essenziale per minimizzare il cammino e i tempi di raccolta. Basti pensare che in un magazzino la maggior parte del tempo (in media il 50%) viene impiegato per la ricerca del prodotto richiesto.
Proprio per questo può essere vantaggioso mappare l’area di stoccaggio, suddividendola in classi, ed analizzare lo storico delle attività di magazzino per individuare in che area posizionare una determinata unità di carico. In ogni magazzino, infatti, esiste una zona facile e veloce da raggiungere, vicina al sito di imballaggio e di spedizione, dove posizionare i prodotti più richiesti.
Mappare il magazzino per aumentare l’efficienza: l’analisi ABC
Una delle tecniche più utilizzate per mappare il magazzino è l’analisi ABC. La tecnica consiste nella suddivisione del magazzino in tre aree. Nella classe “A”, che corrisponde all’area di deposito più facile da raggiungere, vengono posizionate le unità di carico con una probabilità elevata di essere prelevate, mentre nella classe “C”, l’area più remota del magazzino, vengono posizionati gli articoli con una bassa probabilità di essere prelevati.
Un modello per ottimizzare i magazzini automatizzati
Per aumentare l’efficienza del magazzino, dunque, basterebbe effettuare una riorganizzazione periodica, allo scopo di minimizzare il cammino per il recupero degli articoli richiesti.
A tal fine è stato sviluppato un modello che permette di simulare la riorganizzazione e di visualizzare i vantaggi di cui gode un magazzino riorganizzato in base al portafoglio ordini (l’insieme degli ordini di diversi clienti) andando a stimare il tempo e gli spostamenti necessari.
Considerando di voler riorganizzare un magazzino automatizzato suddiviso secondo l’analisi ABC, è necessario conoscere lo stato iniziale del magazzino, ovvero come sono disposti gli articoli e il portafoglio ordini (reale o ipotetico), quali articoli sono richiesti dal cliente e in che quantità.
Nel caso in cui il portafoglio ordini sia noto a priori, gli articoli che lo compongono hanno una probabilità massima di essere prelevati, quindi gli “n” articoli richiesti devono trovarsi nelle prime “n” posizioni del magazzino. Il modello restituisce uno stato desiderato del magazzino che contiene nelle prime posizioni tutte le unità di carico richieste dal cliente, in modo da diminuire i tempi di evasione degli ordini. In questo modo la ricerca degli articoli non dovrà essere fatta su tutte le posizioni del magazzino, ma solo tra le prime “n” posizioni e diminuirà anche il cammino del robot.
Oltre allo stato desiderato del magazzino, il modello restituisce una lista delle movimentazioni ottimizzata, che il trasloelevatore deve effettuare autonomamente per far transitare il magazzino dallo stato iniziale allo stato desiderato. Si parla di lista delle movimentazioni ottimizzata perché `e generata in modo da minimizzare il cammino del trasoelevatore e, di conseguenza, i tempi di riorganizzazione e i relativi costi; una lista delle movimentazioni ottimizzata impiega mediamente un tempo di riorganizzazione inferiore del 20%.
Lo stato finale del magazzino permette di evadere più velocemente il portafoglio ordini considerato.
L’analisi, dunque, permette di stimare il tempo di evasione del portafoglio ordini e confrontarlo con il tempo impiegato ad evaderlo senza effettuare la riorganizzazione, ottenendo così una stima dei vantaggi.
I vantaggi di un magazzino automatizzato che esegue una riorganizzazione periodica sono numerosi e il parametro su cui incide maggiormente è il tempo di evasione di un ordine. Grazie alla lista delle movimentazioni da effettuare per riorganizzare il magazzino, considerando le sue caratteristiche, è possibile valutare i costi della riorganizzazione di quest’ultimo, in modo da programmarne al meglio la periodicità ed aumentare l’efficienza delle operazioni.
Il tema è trattato approfonditamente nella tesi di laurea "Un modello per l'ottimizzazione di riposizionamento merce in magazzini automatizzati" di Andrea Arnone.