Automated warehouses: a model for optimizing the repositioning of goods
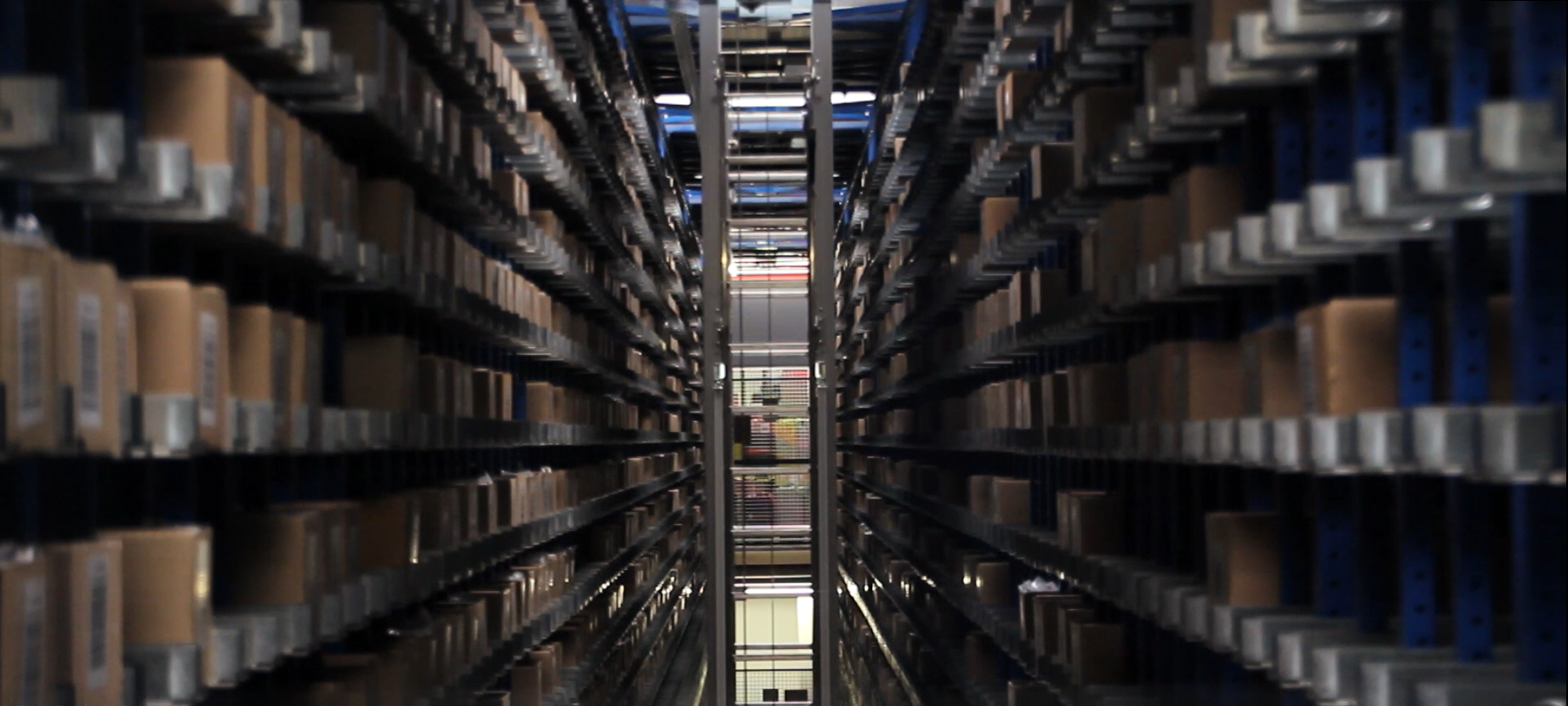
Today, the quality and price of products are not enough to be competitive. it is, in fact, necessary to offer the customer an excellent service, characterized by punctuality and frequency of deliveries.
Therefore, the role of logistics within corporate strategies has become increasingly important: those who excel in this area have a better chance of being competitive in the global market. To achieve this goal, warehouse management becomes a decisive element and, in the case of automated warehouses, a valid goods repositioning model can make a huge difference in terms of costs, time-saving and efficiency.
The warehouse: a company's operational center
The warehouse is indeed a company's operations center, the place where most of the logistics activities happen. It is not only the place where goods are received, positioned, stored and shipped. It is also the crossroads for economic, strategic and promotional values. The warehouse is the heart of the company.
This significantly affects the costs incurred and the level of service expressed to customers. Good warehouse management can lead to:
- reduction of storage spaces
- reduction of costs
- optimization of the handling and processing times of the articles
- increased competitiveness
Numerous activities animate the life of a warehouse and among these, the most expensive in terms of time and money is certainly picking, which means selecting, partially picking and grouping the load units to be shipped to the customer.
The optimization of the arrangement, that is the space to be assigned to each load unit, is an essential element to minimize the journey and collection times. Suffice it to say that in a warehouse most of the time (on average 50%) is spent searching for the required product.
Precisely for this reason, it may be beneficial to map the storage area, dividing it into classes, and analyze the history of warehouse activities to identify in which area to place a certain load unit. In fact, in each warehouse, some sectors are easier and quicker to reach, close to the packaging and shipping site, where the most requested products can be placed.
Mapping the warehouse to increase efficiency: ABC analysis
One of the most used techniques to map the warehouse is ABC analysis. The technique consists of dividing the warehouse into three areas. In class "A", corresponding to the easiest to reach storage area, the loading units are positioned with a high probability of being picked up, while in class "C", the most remote area of the warehouse, the items with a low probability of being picked up are placed.
A model for optimizing automated warehouses
To increase the efficiency of the warehouse, the starting point is to carry out a periodic reorganization, to minimize the path for the recovery of the required items.
To this end, a model has been developed that allows to simulate the reorganization and view the advantages enjoyed by a warehouse reorganized based on the order book (the set of orders from different customers) by estimating the time and travel required.
In the hypothesis of reorganizing an automated warehouse divided according to the ABC analysis, it is necessary to know the initial state of the warehouse, or how the items and the order book (real or hypothetical) are arranged, which items are requested by the customer and in what quantity.
If the order book is known in advance, the items that compose it have a maximum probability of being picked up, therefore the “n” items requested must be in the first “n” positions of the warehouse. The model returns the desired state of the warehouse that contains in the first positions all the load units requested by the customer, to reduce the order fulfilment times. In this way, the search for the articles will not have to be done on all the positions of the warehouse, but only among the first “n” positions and the path of the robot will also decrease.
In addition to the desired state of the warehouse, the model returns an optimized list of movements, which the stacker crane must carry out autonomously to move the warehouse from the initial state to the desired state. This means an optimized movement list, because it is generated in such a way as to minimize the path of the stacker crane and, consequently, the reorganization times and related costs; an optimized movement list takes on average a 20% shorter reorganization time.
The final state of the warehouse allows the order portfolio to be processed more quickly.
The analysis allows to estimate the order backlog fulfilment time and compare it with the time taken to fulfil it without carrying out the reorganization, thus obtaining an estimate of the benefits.
The benefits of an automated warehouse that carries out a periodic reorganization are several, and the parameter that affects the most is the time to fulfil an order. Thanks to the list of movements to be carried out to reorganize the warehouse, considering its characteristics, it is possible to evaluate the costs of the reorganization of the latter, to better plan the periodicity and increases the efficiency of the operations.
The topic is dealt with in depth in the thesis "A model for the optimization of the repositioning of goods in automated warehouses" by Andrea Arnone.