Predictive analytics nel manufacturing: come trasformare i dati in valore e ridurre i costi
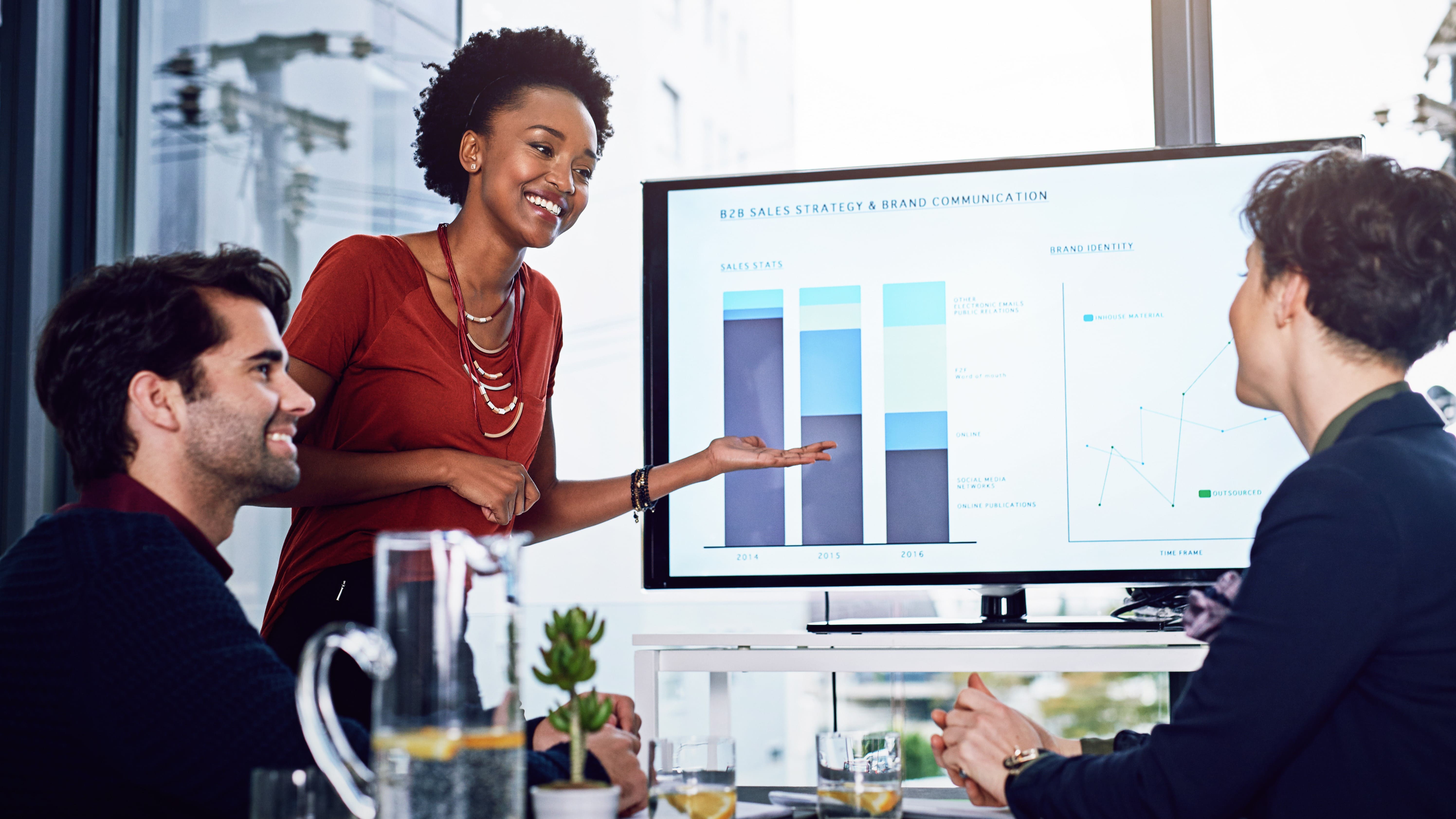
Le industrie del Manufacturing devono continuare a investire in trasformazione digitale per garantire competitività e resilienza nel prossimo futuro. È l’indicazione che emerge da una ricerca di Deloitte, che evidenzia come sia proprio la tecnologia a fornire strumenti per affrontare le sfide del settore. Su tutte, l’incertezza economica e i ripetuti malfunzionamenti della catena di approvvigionamento. La risposta delle aziende è netta: il 76% decide di adottare strumenti e pratiche di digitalizzazione per ottenere, da un lato, una maggiore trasparenza e visibilità nella propria attività produttiva, e, dall’altro, migliorare le performance operative e contenere i costi. La predictive analytics si pone come una delle soluzioni più promettenti per l’intera filiera.
Già nel 2022, infatti, Il World Economic Forum indicava come obiettivo strategico per la Supply Chain e il Manufacturing lo sfruttamento del patrimonio informativo dell’azienda, di cui la predictive analytics rappresenta lo fase più matura. Da un punto di vista tecnologico, ciò significa applicare algoritmi di Artificial Intelligence all’insieme combinato di basi dati storicizzate e informazioni raccolte in tempo reale, il cui esito è la capacità di anticipare le situazioni future e, quindi, di allocare le risorse in modo ottimale.Predictive Analytics nel Manufacturing: come si fa
I processi produttivi del Manufacturing generano una vasta mole di informazioni, rendendo le aziende del settore ottime candidate per l’applicazione della predictive analytics. Aspetti, quali, ad esempio, la gestione della qualità dei prodotti, la manutenzione degli impianti, il throughput degli addetti, o, infine, la gestione dell’inventario, possono ottenere grande beneficio dall’applicazione degli algoritmi previsionali, con l’utilità, pressoché immediata, di ottimizzare le operazioni e abbattere i costi. A tali vantaggi si affianca la possibilità di prevedere le richieste del mercato e analizzare i feedback dei clienti; ciò consente di creare nuovi servizi (servitization), migliorare la Customer Experience e aumentare la fidelizzazione.
Nei diversi ambiti citati, la predictive analytics segue un processo in 5 step:
- Raccolta e preparazione dei dati. Le informazioni storicizzate e in tempo reale provenienti da diverse fonti (sensori IoT, macchine di fabbricazione, ERP, software di produzione, ecc.) vengono collezionate, trasformate e normalizzate per renderle coerenti e utilizzabili nei modelli predittivi.
- Individuazione dei pattern. Una volta che i dati sono stati preparati, l'analisi combinata delle informazioni provenienti da fonti multiple permette di identificare schemi e tendenze ricorrenti. Questa fase è fondamentale per riconoscere correlazioni che potrebbero non essere evidenti senza un'analisi approfondita. L'intelligenza artificiale gioca un ruolo cruciale in questa fase, individuando pattern complessi e potenziali anomalie che possono influenzare il processo decisionale..
- Validazione e ottimizzazione del modello. Prima di applicare i modelli predittivi, è essenziale validarli utilizzando dati storici per verificarne l'accuratezza. Il modello viene testato per assicurarsi che sia in grado di effettuare previsioni affidabili. Successivamente, può essere necessario ottimizzarlo per migliorare le prestazioni, assicurando che eventuali variazioni nei dati non compromettano la qualità delle previsioni. Questo passaggio è fondamentale per evitare sovra-adattamenti (overfitting) o modelli troppo semplicistici (underfitting).
- Applicazione del modello predittivo. Una volta validato e ottimizzato, il modello predittivo viene applicato ai dati per fornire previsioni operative utili. Questa fase consente, per esempio, di prevedere guasti di macchinari in ambito di manutenzione predittiva, oppure di stimare la domanda di produzione o gestione delle scorte. I risultati delle previsioni possono essere integrati nei processi aziendali per migliorare l'efficienza, ridurre i costi e ottimizzare le risorse.
- Monitoraggio e aggiornamento continuo. I modelli predittivi non sono statici: richiedono un monitoraggio costante e aggiornamenti regolari per mantenere la loro efficacia nel tempo. Man mano che vengono raccolti nuovi dati e cambiano le condizioni operative, il modello deve essere rivisto e aggiornato.
Questo approccio consente alle aziende del Manufacturing di evitare i fermi macchina (manutenzione predittiva degli impianti), di prevedere i livelli qualitativi dei prodotti o di ottimizzare gli approvvigionamenti in base alle previsioni delle richieste di mercato.
Già nel breve periodo, ciò si traduce in abbattimento dei costi, come documentano diversi case study. Con la manutenzione predittiva degli impianti, infatti, gli interventi avvengono secondo necessità; la maggiore qualità dei prodotti diminuisce i resi e abbatte gli sprechi; la gestione ottimale delle scorte, infine, evita gli acquisti in eccesso (o in urgenza, con costi potenzialmente maggiori) di materiali e componenti.
Predictive analytics: casi d’uso
Diversi case studies hanno dimostrato come la valorizzazione dei dati aziendali porti benefici tangibili alle aziende del Manufacturing, quali, ad esempio, l’ottimizzazione delle performance, la riduzione dei costi, l’ottimizzazione della Supply Chain o il miglioramento della Customer Experience. Ecco alcuni dei casi d’uso più significativi:
- Ford Otosan. L’azienda automotive di Istanbul ha digitalizzato le fabbriche creando modelli digital twin per circa il 50% delle linee di produzione della carrozzeria. I dati della sensoristica, dei volumi di produzione, delle percentuali di guasto e della produttività degli operatori, sono stati inseriti in una piattaforma Big Data per eseguire l’analisi dei colli di bottiglia e identificare le fasi critiche del processo. In un momento successivo, la predicitve analytics è stata impiegata per simulare nuovi layout delle linee produttive. Tale processo ha generato un incremento di produttività degli addetti pari al 15%, e la riduzione dei tempi di ciclo corrispondente al 15%.
- Henkel. La multinazionale del settore chimico ha impiegato la predictive analytics per ottimizzare le rotte di spedizione e la consegna delle merci. L’analisi di un numero elevato di parametri relativo al transito e alla posizione effettiva delle merci, per ottimizzare l'uso della banchina e ridurre il fermo delle merci, con dashboard di visualizzazione a livello SKU - Stock Keeping Unit. La predictive analytics viene impiegata per anticipare e ottimizzare le prestazioni del singolo vettore, riducendo i tempi di permanenza. Tale processo ha generato un risparmio del 12% dei costi logistici e la riduzione del 50% delle penali dei clienti.
- ZF Friedrichshafen. La multinazionale specializzata in componentistica per i trasporti raccoglie dati provenienti da fonti diverse (sensoristica delle linee di produzione, computer vision, ERP aziendale e MES – Manufacturing Execution System) per risalire ai difetti di fabbricazione, anticipare possibili imperfezioni future e controllare la sicurezza degli impianti. Le grandi moli di informazioni sono raccolte, normalizzate e visualizzate da strumenti, quali, ad esempio, Microsoft Power BI, al fine di fornire actionable insight ai manager della produzione. L’esito, tra gli altri, è stato l’abbattimento dei costi di esercizio pari a 65mila €/anno per ogni plant.
In uno scenario caratterizzato da incertezze a più livelli (slowdown economico, inefficienze della Supply Chain, evoluzione dell’offerta di mercato, ecc.), la predictive analytics fornisce alle aziende approcci pratici per affrontare tali sfide: decisioni di business informate, riduzione dei costi e performance degli impianti produttivi garantiscono la massimizzazione dei margini e lo sviluppo dell’offerta, secondo le esigenze di un mercato in continua evoluzione.