Control 1st leads the Transition 4.0: Del Curto case history
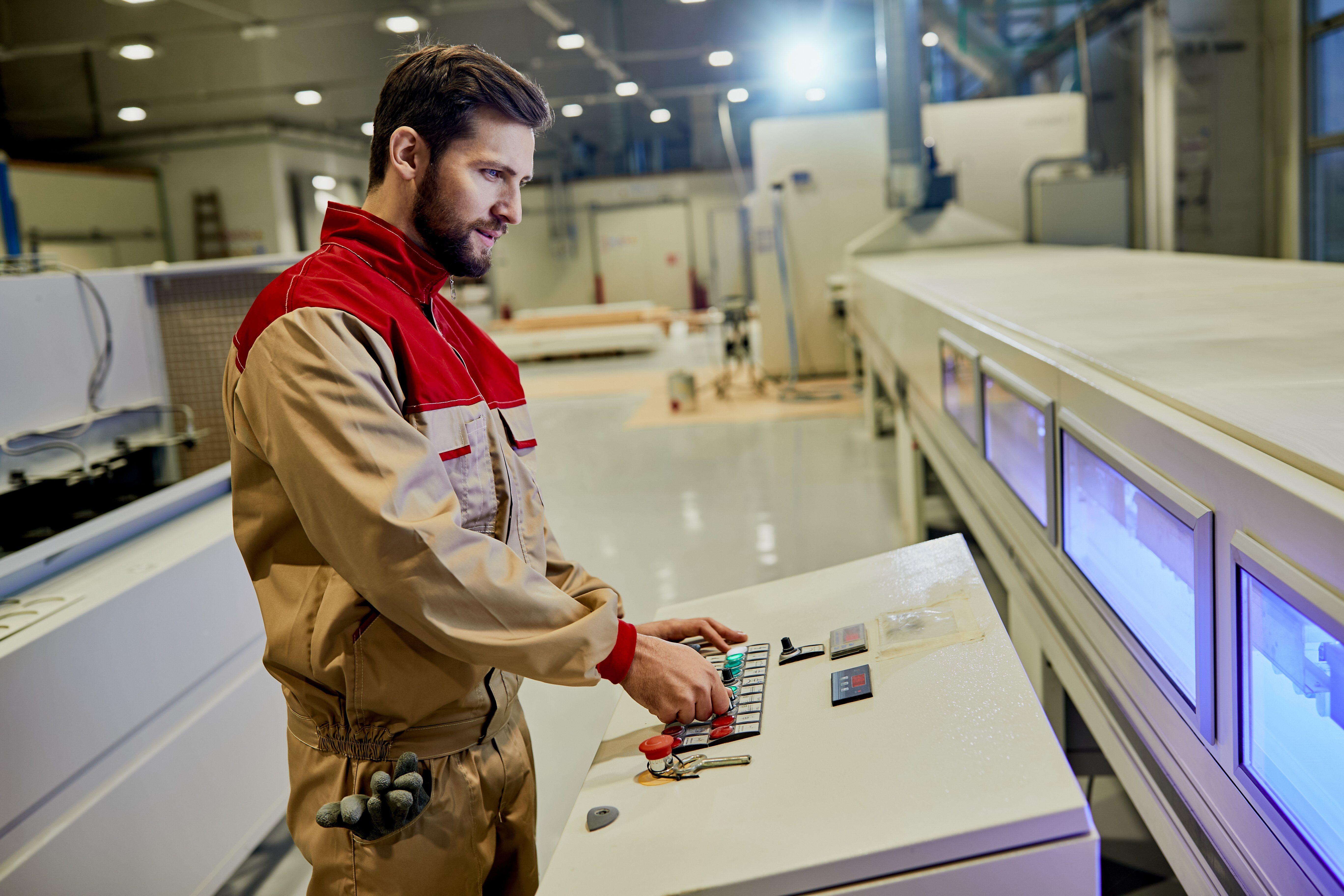
The Transition 4.0 incentives shifted the focus on a new priority: supporting companies in their technological and Digital Transformation processes. Strengthening the competitiveness of the production system, increasing the rate of digitization, technological innovation and internationalization of high-tech sectors is the key objective for the coming years.
In this context, investing in industrial automation can bring important benefits. New technologies, in fact, contribute to improving working conditions and increase productivity and operational efficiency.
Transition 4.0: incentives to improve industrial automation
13.381 billion euros is the sum allotted by Italian government for the Transition 4.0 Plan. The plan aims to promote industrial research, technological upgrades and the Digital Transformation of production processes and investment in intangible assets; The plan is an evolution of the Industry 4.0 paradigm, and it opens these funds to a larger number of beneficiaries.
Control 1st, Beta 80 Group's innovative Incident Mastery Platform, was the technological tool chosen by Del Curto S.r.l to embark on its Digital Transformation journey, leveraging the benefits of the abovementioned Transition 4.0 Plan.
Del Curto: renovating the industrial plant from an IT perspective
Del Curto S.r.l., a Brianza-based company specializing in wood recycling and pellet production, chose our Control 1st platform for its Transition 4.0 journey. A path started with an analysis of the main issues and evolved through a customization and integrations with specific machinery.
The project featured a combination of perspectives, knowledge and skills related to the industrial automation world which, combined with our extensive experience of Control Room technology, made it possible to promptly map and respond to the customer’s needs.
Unified management of industrial machinery
Del Curto’s Digital Transformation aimed to integrate all its machinery through the Control 1st platform.
Del Curto had three specific needs:
-
to digitalize the production plant
-
to merge all information produced by industrial machinery into a single database
-
to have full control of its industrial processes
The choice to introduce new technology tools to generate more value proved successful.
Control 1st and Industrial Automation: the new potential of the platform
The project had its complexities; mainly the integration of Control 1st with the preexisting machinery, designed and installed by different vendors and with different protocols. The platform was able to organize and integrate all the different tools and data sources seamlessly.
This was the first time Control 1st was used in an industrial automation field, allowing Del Curto to perfectly integrate machinery from different manufacturers, centralizing information, executing direct commands on production cycles, historicizing data, and highlighting production insights.
Control 1st, the innovative Mastery Platform favored the unified control of technological resources and their correlation with operational processes, supporting the customer in data collection and interpretation.