Process automation in Kyocera with Beta 80
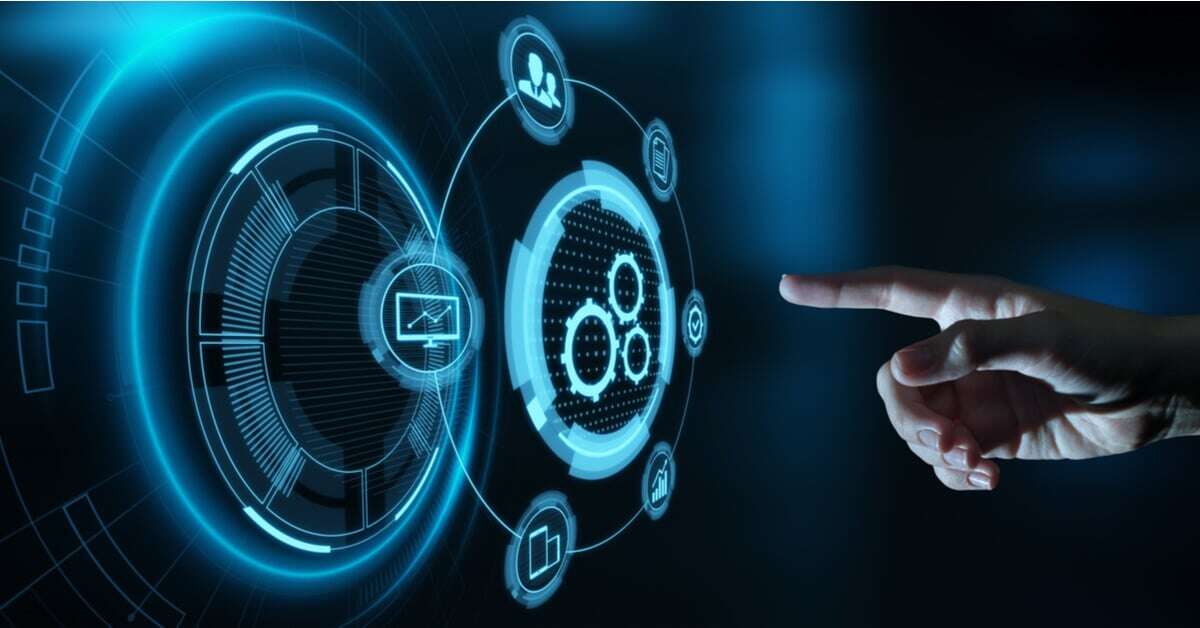
The process automation adopted by Kyocera Document solutions Italy, part of the well-known giant leader in multifunctional systems and printing materials, is emblematic of the methodology developed by Beta 80 in RPA (Robotic process automation) projects. This methodology starts from the assumption that the business processes eligible for automation, thanks to 3 phases of Quick Assessment (selection, qualification, roadmap), must be identified before the implementation and release of the solution itself. RPA systems, in fact, work when one does not move from the generic intent of wanting to automate certain activities, but rather from a precise and well-defined need that has a clear link with a business value. In the case of Kyocera, the need arose when the Italian division of the group had to deal with the management of public administration orders that pass through the Consip platform, the instrumental body of the Ministry of Economy and Finance which coordinates all PA purchases. These also include Kyocera's: printers, cartridges, toners and related equipment.
Kyocera facing Consip order management
Any municipality or public body, which needs to procure ICT tools and technologies, can do so by connecting to the Consip website. Kyocera, as a winner of some lots banned by the company wholly owned by MEF, was called upon to manage this flow for the supply under its responsibility. By accessing the same portal used by the buyers, therefore, he had to download the orders, verify the consistency with his offer, ascertain the formal correctness of the request, and then proceed to the subsequent steps of entering the request in his own management system. At the beginning of 2019, however, the last lot assigned by Consip had provided that public administrations could make multiple purchases at the same time. This circumstance prevented the automation of the process, the automatic passage of the order to the software that was supposed to process it, forcing Kyocera to take another step of manual control. With a slowdown in terms of efficiency and an increase from the point of view of the human resources to be involved. This is where Beta 80's expertise in RPA solutions comes into play.
The RPA method of Beta 80: fast analysis for fast results
Beta 80 launches the process automation project in mid-2019, making use of Automation Anywhere, the RPA architecture proposed by IBM of which Beta 80 is a business partner. After a quick preventive analysis, which is not by chance an integral part of its methodology based on Quick Assessment, within a couple of months, between August and September, Kyocera can begin to process a certain type of order automatically. On this basis, then, improvements are added in the course of work to make the robot or bot software increasingly "intelligent". These subsequent releases are also typical in an appropriate approach to the RPA world, even in the presence of a favorable situation, such as that of Kyocera, in which the processes to be automated are clearly identified. Beta 80 knows this due to the long experience gained in this field and it is for this reason that its method in the RPA field is inspired by the “agile” one sometimes used in software development. In other words, it is focused on achieving results in the shortest possible time.
The benefits brought to Kyocera by the automation of processes
The first result, since the first version of the bot, consisted in clearing backlogs and optimizing the management of hundreds of orders. The second concerned the enhancement of the human capital employed in the pitching office, which was relieved of the repetitive tasks performed by the bot. The third was appreciated by Kyocera managers in the critical period caused by the Covid-19 epidemic. An unforeseen event that today it is possible to cope with the support of a bot that daily downloads orders, processes them, compiles the Excel files, highlighting only any anomalies or discrepancies. Confirming the fact that RPA technology does not replace man and does not steal his work, but allows to increase the efficiency and effectiveness of a process and, therefore, of the people involved in the process itself. People who, with the last stage of the project due to be completed in 2020, will be even more able to pilot the bot, so that it responds better and better to the needs from which Kyocera's request for process automation was born.